LIGHT UP YOUR CAREER
What we do
Development
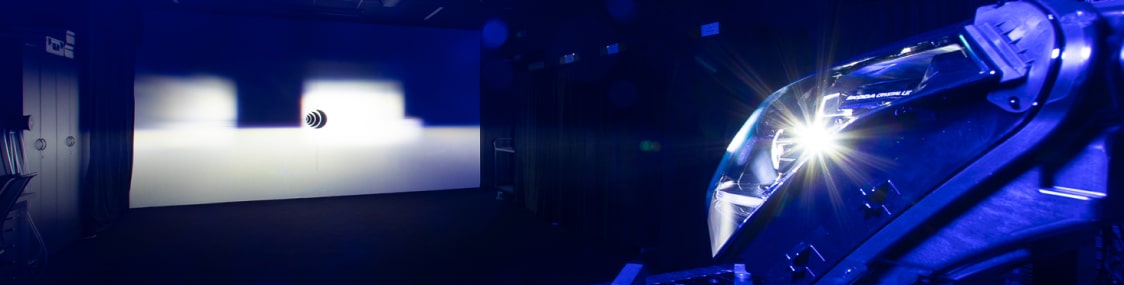
Our development department includes teams for headlamps and projection modules development, optics development, design, simulation, and project management. The development process also involves testing laboratories and a prototype workshop. Read more
Additionally, our development scope includes a specialized department within the FORVIA HELLA world—Electronics Development, focusing on embedded hardware and software. Since 2018, we have held global responsibility for the development of rear lamp electronics.
Free positions in development and designProduction of assembly lines
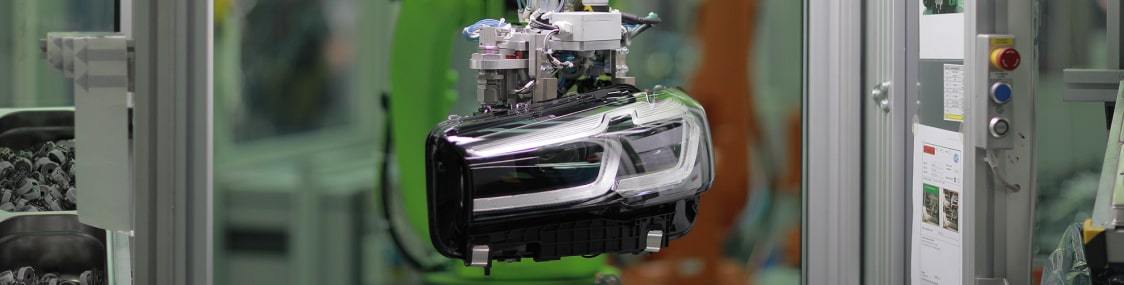
The production plant also includes a department dedicated to the development and manufacturing of machines and equipment.
This is a unique department that cannot be found elsewhere in the broader region. Internally, we call it VMK, originally derived from the German term Vorrichtung Maschinen Konstruktion. VMK supports not only the Mohelnice plant but also builds production lines for other FORVIA HELLA locations worldwide.
Based on customer requirements, it designs optimal processes and equipment for assembling headlamps and lighting systems.
All necessary machines and equipment are designed, manufactured, assembled, electrically connected, and programmed in-house.
Manufacturing
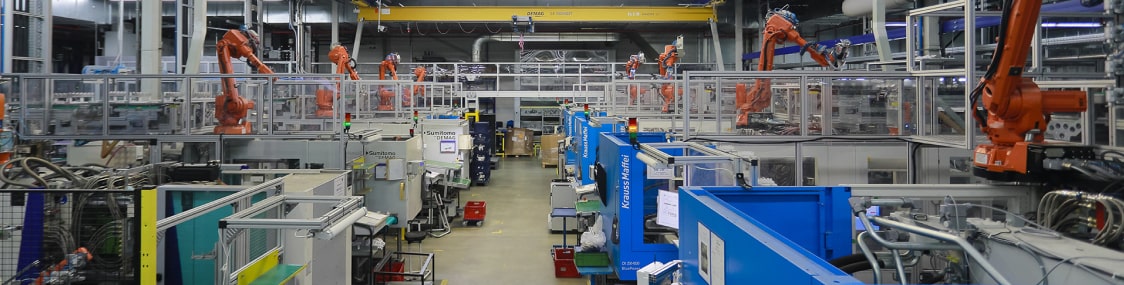
We have the most automation-laden plant far and wide, filled with hundreds of robots from various manufacturers—including collaborative ones. That’s why our technical service includes a dedicated department solely focused on automation. Additionally, our in-house department for the development and production of assembly lines provides strong support. This means we not only have a huge machinery fleet but, more importantly, a strong foundation of dozens of experienced professionals and programmers. However, we’re not resting on our laurels—we continue to expand our automation capabilities.
Free positions in manufacturingTesting
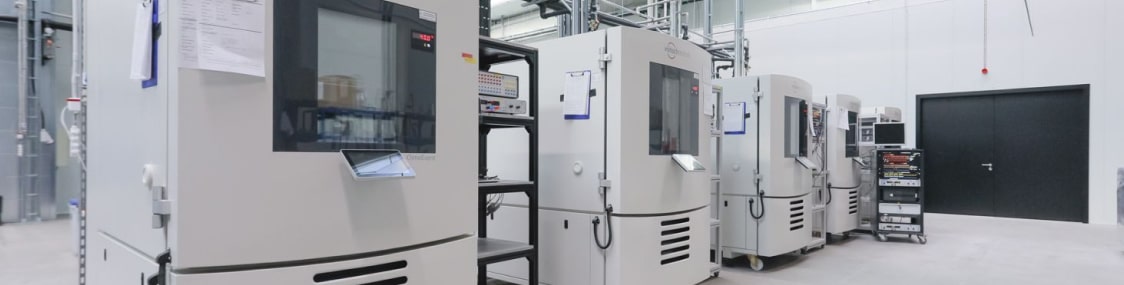
Products must undergo thorough testing to meet customer specifications as well as legal requirements. Our testing laboratories carry out for example climate, vibration, material, chemical or durability tests. Climate testing includes assessing the effect of temperature differences on our products and the overall lifetime of the headlamp. Corrosion tests examine the effect of salt on external metal parts. Vibration stress tests test the product's resistance to mechanical shock, for example. Read more
Since today's modern headlamps are packed with electronics, the functionality of individual electronic components and entire headlamps and lamps is also tested. Electromagnetic compatibility is also checked to ensure that our products do not affect other objects in the car, including themselves, and that they can withstand the effects of other devices. An important part of this is 3D measurement, which is used to verify dimensions. Some of our laboratories also fall under the ISO 17025 accreditation process.
Free positions in testing laboratorySpare parts
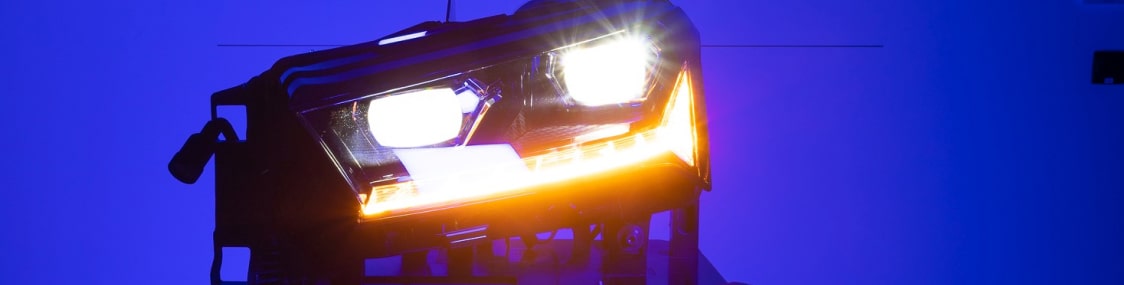
In Olomouc, we produce spare parts. Production lines that are no longer used for serial manufacturing are relocated here. These include a variety of headlamps from multiple brands, which we will continue to manufacture for another ten to fifteen years after serial production ends.
Free positions in Olomouc